Risk Management and Hazard Control
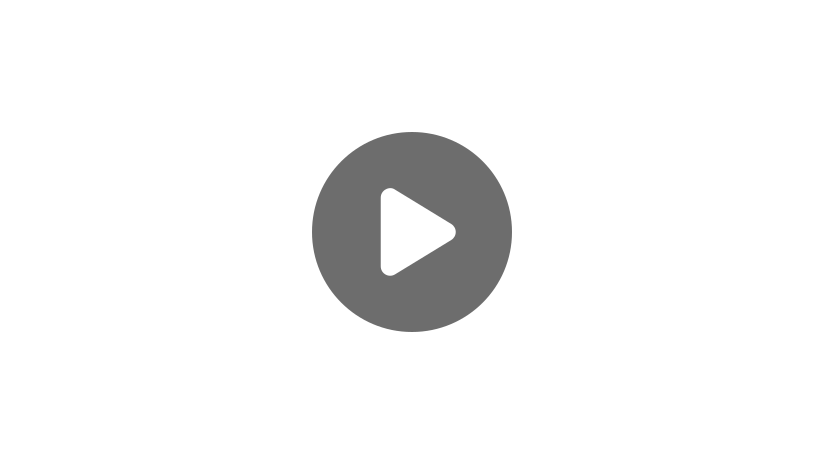
Hey guys. Welcome to this video on Risk Management and Hazard Control Process. Risk management and hazard control are some of the most important issues to familiarize yourself with to help ensure the safety of all those around you. There are several different topics to be covered on this subject, but in this video I will cover the issues that will help to prevent any imminent danger.
ANSI/AIHA Z10
Purpose:
The purpose of the ANSI/AIHA Z10 is to lay out a framework for an effective occupational health and safety management system. The main elements of the standard require management commitment to the implementation of the standards. This is demonstrated by:
– participation of the organization’s employees in the occupational
health and safety system,
– risk assessment,
– planning of the occupational health and safety system to address
the risks identified,
– evaluation of the system and appropriate corrective action.
The system is completed by management review to assess achievement of objectives and adjustment of targets.
Main objectives:
The main objective of the ANSI/AIHA Z10 American National Standard for Occupational Health and Safety Management Systems is to set a framework for a management system. This systemic approach, while it encompasses compliance as a foundation, seeks to evaluate the organization’s risks holistically, and to respond to them in a proactive way rather than a reactive manner. The objective is to identify risks before they result in injury or harm, and systematically engage various elements of the organization in planning for risk management. The organization then evaluates its progress and performs root cause analysis to provide corrective action. This management system serves the overall objective to create a safe workplace that goes beyond compliance.
Importance of safety
First of all, safety is important for a humanitarian reason. We have a moral responsibility to keep employees, co-workers, customers, and society in general safe. Second, safety is important for a legal reason. We are obligated by laws and regulations to meet certain safety standards. These laws and regulations are necessary because different people have different definitions and standards for safety. The laws and regulations provide common standards for everyone to follow. Third, safety is important for a cost reason, including both the cost of human life and property. Cost calculations need to include money spent paying for both of the following: The negative consequences of poor safety (such as injuries and damaged equipment); and preventive measures to minimize safety problems.
Principles of hazard control, recognizing hazards, and selecting preventive actions.
The first two principles of hazard control are: Recognize hazards & Select preventive actions.
Recognizing hazards usually requires a team approach, as no one person can know all the possible hazards. This step includes such tasks as knowing how materials interact, understanding the use environment, and anticipating user behavior patterns.
Selecting preventive actions can include:
design, material, etc.
– Reducing the severity of the hazard.
– Reducing the probability that the hazard will occur.
– Designing redundancy into the system through backup systems,
parallel subsystems, etc.
– Installing safety devices such as machine guards and
fail-safe devices.
– Installing warning devices.
– Developing safe procedures.
– Requiring personal protective equipment.
Heinrich’s axioms of industrial safety
Heinrich’s ten axioms of industrial safety are as follows:
including the accident that caused the injury.
2. Accidents occur because of a person’s unsafe act and/or a
mechanical or physical hazard.
3. Most accidents are caused by people’s unsafe behavior.
4. Unsafe acts and conditions don’t always immediately result
in an accident.
5. Knowing why people commit unsafe acts can help determine
corrective actions.
6. Most accidents are preventable.
7. Accident prevention techniques work hand in hand with quality
and productivity techniques.
8. Safety should be a management responsibility because management
can ensure the best results.
9. Supervisors play a key role in preventing industrial accidents.
10. Both direct and indirect costs result from accidents.
Petersen’s accident/incident theory
The accident/incident theory is an outgrowth of the human factors theory. It includes additional elements such as:
– Decision to err.
– Systems failure.
According to the theory, ergonomic traps (such as workstations that are the wrong size) and a conscious or unconscious decision to err combine with overload to lead to human error, which in turn can lead to an accident. Systems failure becomes a factor when systems that could mitigate the human error and prevent an accident fail. These systems can include policies, procedures, training, and inspections.
Common causes of accidents
The most common causes of accidents, according to Hartshorne, include the following:
rules and procedures, etc.
– Decision to work unsafely.
– Mismatch or overload – worker is in poor physical condition or is stressed
and tired, the work is too complex or too repetitive, the work environment
is too hot or noisy, etc.
– Systems failure – management failure to provide clear policies and procedures,
to correct hazards, to offer training, etc.
– Traps – poorly designed workstations, defective equipment, inadequate lighting
and ventilation, etc.
– Unsafe conditions
– Unsafe acts
Approaches to accident prevention
A reactive approach to accident prevention has four basic steps:
2. An investigation takes place.
3. Results from the investigation are analyzed.
4. Preventive measures are put into place to prevent
the accident from happening again.
In this approach, an accident must occur first before preventive measures are put into place. A proactive approach to accident prevention tries to keep accidents from occurring in the first place. This approach has two steps: 1. Analyze potential accidents. 2. Put preventive measures into place to prevent the accidents from occurring.
Both approaches rely on concepts of frequency, severity, and cost to set priorities.
A frequency strategy focuses on reducing the accidents that occur most frequently. A severity strategy focuses on reducing the accidents that cause the most serious injuries or most damage. A cost strategy focuses on reducing the accidents that are the most expensive.
Accident prevention theories
The Errors in Management System theory was developed to show the relationship between management and safety. They define an accident as a type of error that interrupts the normal process of work. They further theorize that most errors – as many as 85% – result from poor processes and procedures developed by management. Workers are simply following the processes they have been given and therefore cannot avoid making and repeating the error. According to this theory, safety programs should focus on improving processes in order to reduce or eliminate errors. Ideally, management and workers should work together to develop safe and productive processes.
The Multiple Factor Theory postulates that accidents are generally caused by many factors working together. The factors change from one incident to another but can generally be classified as one of the four Ms defined by Grose:
– Machine (equipment and vehicles, including construction materials,
placement of controls, energy sources, etc.).
– Media (environment, road conditions, and weather, such as pollution,
snow on the road, fresh vs. salt water, etc.).
– Management (organizational structure, policies, procedures, etc.).
By examining the relationships among these factors, one can analyze processes and procedures and identify ways to prevent or reduce accidents.
Haddon proposed the Energy Theory, which that accidents and injuries often involve energy transfer. Motor vehicle accidents are an example of this type of accident. The theory further states that the severity of injuries is related to the following: The amount of energy transferred. The way the energy is transferred. The speed at which the energy is transferred.
Domino Theory
According to the Domino Theory developed by Heinrich, the sequence of events in an accident can be compared to a series of five dominoes:
2. Undesirable traits such as carelessness, violence, or
unsafe habits, leading to an…
3. Unsafe act or condition, which causes an…
4. Incident, which leads to an…
5. Injury
According to this theory, removing any of the earlier dominoes can prevent an injury. The theory especially emphasizes removing the unsafe act or condition: domino number three. The limitation of the domino theory is that it is often too simplistic: many accidents have multiple causes. By relying on the domino theory, a safety program may identify just one primary cause of an incident, ignoring other causes and underlying factors.
Control methods
Financial justification is the process of making a business case for an investment. It may at first seem that it is difficult to make financial justification for safety improvements. While it is true that it is difficult (and not desirable) to place a monetary value on human life, there are quantifiable cost savings (and, therefore, a financial justification) for implementing improved control of safety hazards. Financial justification can be made for the impact reduced frequency and severity of injuries can have on worker’s compensation costs and employee lost time and reduced productivity. Financial justification can, also, be made for better control of work processes that result in reduced cycle time while improving ergonomic factors. In the bigger picture, improvements in safety can quantifiably contribute to decreased employee turnover. Decreased employee turnover saves money for training and results in an improved product due to fewer employee mistakes.
Hierarchy of controls
The hierarchy of controls refers to a preferred top-down solution to safety control methods. In order of most to least desirable, they are elimination, substitution, engineering, administrative/work practice, and personal protective equipment (PPE) controls. When considering how to control a risk or hazard, one should always start with the most desirable— eliminating the hazard altogether. For example, can a tool be used to eliminate the ergonomic hazard? Then, consider substitution—can a less toxic chemical be substituted for a toxic chemical? If substitution cannot work, then can the hazard be engineered away? For example, can we install ventilation to remove the airborne toxic emission so employees will not be exposed to toxins? If engineering will not work, or is not effective enough, we must then consider administrative controls, such as job rotation to diminish the risk. As a final control method, PPE is employed to protect employees from the risk. It is evident that PPE is often employed so there is room for improvement in industry to control risk at a higher level on the hierarchy.
Worker’s compensation insurance
Worker’s compensation insurance is similar to other types of insurance in that a company will pay a premium to an insurance company that will then pay the actual costs of the injured worker (for replacement of lost time wages and physician visits). The company benefits in that the premium cost is predictable over the course of the year, regardless of actual costs incurred by the injured workers. However, the insurance companies definitely penalize companies with high injury rates and costs by using both frequency and severity measures to influence the premium cost. Moreover, the data on frequency and severity are compared to others in the same industry, and the result is an experience modification (X-mod) factor that can multiply the premium due by a multiplier greater than 1.0 (or less than, if costs have been well controlled). It is beneficial to the company to partner with an insurance company that is an aggressive partner in closing cases as quickly as possible; this is because, when an injury occurs, the insurance company sets aside a theoretical reserve that they believe is a good estimate of the costs that will be incurred. Those costs are not released until the case is closed, and they continue to influence premium rates.
Proper incident management for worker’s compensation insurance Comprehensive case management should be a part of every company’s risk management and loss control strategy. Although it would seem that the worker’s compensation insurance company would manage cases to control costs, they often do not because their pricing structures enable them to make money by raising premiums more than costs. Working to bring worker’s compensation cases to a close as quickly as possible releases the reserve money allocated to the case and reduces the company’s experience modification factor. Proper case management also includes always offering restricted duty assignments as a way of reducing case costs, challenging any cases that are suspected of not being work related, and managing as many incidents as first aid as can be legally classified as such. Proper case management also includes treating minor injuries before they become major; for example, applying over-the-counter antibiotic cream to cuts or burns before they become infected and require a visit to a physician.
Workers’ compensation laws
Workers’ compensation laws protect workers who are injured on the job. These laws provide payment for lost wages, medical expenses, burial expenses, rehabilitation, and impairments. The laws have six primary objectives: (1) To replace the income a worker misses by being unable to work and to provide prompt medical treatment. (2) To save workers and employers the time, trouble, and expense of litigation. (3) To keep injured workers from turning to public and private charities. (4) To encourage employers to develop procedures that prevent and reduce accidents. (5) To provide workers with rehabilitation so that they can return to work more quickly. (6) To encourage accident investigations not in order to find fault but to prevent similar events from occurring again.
Reducing workers’ compensation claims Workers’ compensation claims pay workers for injuries they receive due to on-the-job accidents. Therefore, any programs that reduce the frequency and severity of accidents will likewise reduce workers’ compensation claims. Some specific strategies safety programs can use include the following: (1) Dealing with the fears and stresses that workers and their families feel after an accident. (2) Building worker confidence. (3) Helping workers rebuild their strength and endurance. (4) Helping workers develop new job skills. (5) Helping supervisors deal with the paperwork, investigation, and other fallout from the accident. (6) Helping supervisors make any necessary job modifications so the injured employee can return to work more quickly. (7) Helping co-workers deal with any negative feelings they have toward the injured worker (including management and labor on safety committees in order to foster cooperation and teamwork). And finally, (8) providing rewards to teams that meet safety goals.
Developing a business continuity plan
A business continuity plan is a written document that plans for continued business operation and provision of services during interruptions due to natural disasters, fires, or pandemic disease outbreaks. A robust business continuity plan has input from operations, upper management, finance, human resources, safety, information technology, and logistics. First consideration should be given to the potential types of disasters, such as fire, flood, tornado, hurricane, earthquake, terror attack, or widespread power or other utility disruption. Critical supplier disruption should also be considered; for example, what alternative suppliers are available? Plans should be made for employee notification, customer notification, restoration of computer systems, restoration of the supply chain, and restoration of transport networks. The documents and telephone contact information should be kept in several locations on and off site and electronically accessible to the management team.
Ergonomics also play a huge role in risk management and hazard control process. To check out our ergonomics video, or other videos, click here.